The usual default for the plastic mold system in injection molding process
- Jussi zhong / plastic mold expert in Shenzhen
- 2015年11月20日
- 讀畢需時 1 分鐘
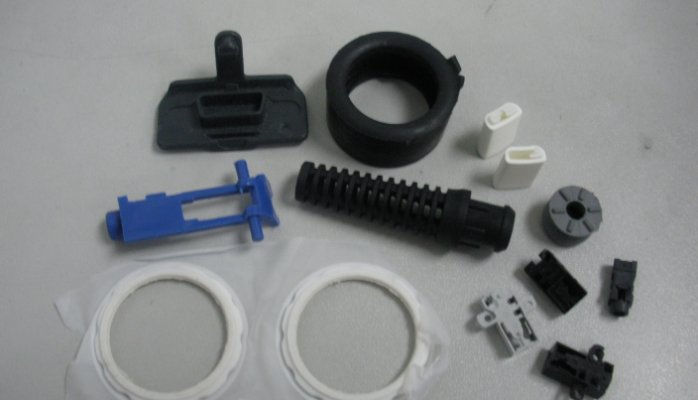
For each mold, we also meet the various issues in the injection molding process. Below are the common issues we often meet.
Position: Cavity
Defaults: stick to the cavity or damage the cavity steel when pick up part Reasons: mold temperature is too high, hold time or pressure is too big, the tool to pick up part inappropriate
Position: core
Defaults: pins broken or plastic part damage core when mold close Reasons: mold temperature is too high, hold time or pressure is too big, the part draft angle is not enough, plastic part haven't been pick out complete when close mold
Position: Runner
Defaults: stick to the cavity Reasons: part draft angle is insufficient, Nozzle radius on the sprue mismatch with the injection machine
Position: Guide pin / Guide bush
Defaults: Wear out Reasons: didn't do good job on lubrication, didn't clean dust, half mold fall down
Position: Ejector
Defaults: Ejector broken Reasons: no lubrication on the ejectors, unbalance of the ejection, the force to stick to part is too big, ejector is too long
Comments